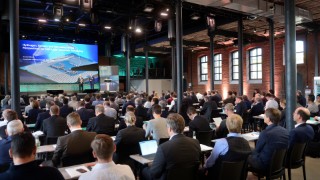
On April 8 and 9, 2025, the UKP workshop will once again open its doors and bring together experts from industry and research at the venue DAS LIEBIG in Aachen. As the most important platform for material processing with ultrashort pulse lasers, this event not only offers visitors the latest insights into technological advances, but also a unique opportunity to discuss the latest applications and solutions.
more info